Delta D2 Diesel Powered Helicopter
Delta Helicopters Introduces The
DELTA D2 HELICOPTER
The First Diesel Powered Helicopter In The World
A two (2) seat utility diesel helicopter designed and built by Australians for the harsh Australian conditions.
Plenty of airlines are testing out biofuels in passenger jets, but helicopters have largely been ignored — until now. Australia-based Delta Helicopters is developing what it says is the first biofuel-capable diesel helicopter in the world using the DeltaHawk DH200 V4 two (2) cycle diesel engine.
It is believed to be the first publicly available, non-turbine, commercially produced diesel engine powered helicopter in the world.
DELTA D2 DIESEL HELICOPTER SPECIFICATIONS | |
---|---|
Maximum Take Off Weight (MTOW) | 955 kg |
Empty Operational Weight (EOW) | 580 kg |
Cruise Speed | 103 kts |
Endurance | 4 hrs |
Horsepower | 180 @ 2650 rpm |
Fuel Consumption | 11.8 GPH @ 180 hp (100%) |
Fuel Consumption | 8.0 GPH @ 135 hp (75%) |
Service Ceiling | 100% Power to 18,000 feet MSL |
Engine Orientation | Vertical |
Fuels | Uses Most Common Jet and Diesel Fuels |
Electrical | 60 Amp, 28 Volt Alternator Standard |
Australia Developing the World’s First Biofuel Capable Helicopter
Courtesy: Treehugger 11 May 2010
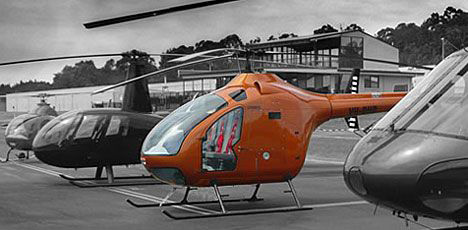
The Bio-diesel capable Delta D2 kit helicopter from Queensland, Australia.
Earlier this year, our transport editor, Mike, pondered the concept of diesel helicopters. Well, they may be closer than he thought. Delta Helicopters of Queensland, Australia, are already prepping their Delta D2 prototype to be the world’s first diesel helicopter.
It is expected that the Delta D2 diesel helicopter will be made available in self-assemble kit form, designed for use by farmers on Australia’s remote farms, who already have diesel on hand for their trucks, tractors and farm machinery. The engine is coming from the US firm DeltaHawk.
They’ve been working on diesel aviation engine that they claim burns 40% less fuel standard gasoline aviation engines and 75% less than turbine aviation engines. Plus they reckon they can get 30-40% more range per gallon. What’s more, a DeltaHawk diesel aviation engine is said to be capable of using biofuels.
It is hoped that “kit sales will assist the funding of the one and a half million dollars required to meet the manual and paper work required to achieve normal category certification.”
The two-seater Delta D2 diesel helicopter was designed by aeronautical engineer Bill Whitney, who has great hopes for the aircraft, “The Delta can generate more torque, which is what helicopters need to keep aloft. They’re less volatile and the fuel is greener than petrol, so the same quantity takes you further.
It isn’t just the four-cylinder, two-stroke, water-cooled, turbocharged diesel engine which will be unique to the Delta D2 diesel helicopter. Though by virtue of that engine by virtue of that engine it will have no spark plugs, no magnetos, no high tension leads, no valves and no head gaskets. It will also have custom made carbon-fibre rotors, semi-transparent fuel tanks, a massive cargo box under the rotor and transparent inspection hatches over critical couplings.
It is expected that a kit will be worth about $180,000 AUD, or $200,000 AUD fully assembled.
First diesel chopper undergoes testing
Courtesy: Australian Flying Magazine 13 May 2010
South East Queensland’s Delta Helicopters hopes to complete testing of its Delta D2 prototype, the world’s first diesel chopper, later this year.
After eight years of developing the Delta D2, the company hopes to finish testing the prototype by August. The two-place Delta D2 could be suitably employed by farmers for mustering operations and aerial property inspections.
“I’m hoping to be able to offer the amateur-built kit side of it by the end of this year in real product,” Delta Helicopters’ Graeme Smith told ABC Online. “We should be ready as far as finishing our testing in about two, maybe three month’s time.”
The Delta D2’s engine, being built by US company DeltaHawk, is a four-cylinder, two-stroke, water-cooled, turbocharged diesel power plant that contains no spark plugs, magnetos, high tension leads, valves, or head gaskets. It also boasts custom made carbon-fibre rotors, semi-transparent fuel tanks, a large cargo box under the rotor and transparent inspection hatches over critical couplings.
DeltaHawk claims the engine burns 40 per cent less fuel than standard aircraft engines and 75 per cent less than turbine engines. The engine, which will be unique to the Delta D2, is also said to be capable of running on biofuels.
“The Delta can generate more torque, which is what helicopters need to keep aloft,” aeronautical engineer Bill Whitney, who designed the Delta D2, explains. “They’re less volatile and the fuel is greener than petrol, so the same quantity takes you further.”
All photos courtesy: Delta Helicopters unless otherwise specified.
EDITOR: I have been contact with Delta Helicopters (December 2015) who have advised they have many hurdles to cross before there product will commence further towards production. The primary concern is the availability of the DeltaHawk DH200 V4 diesel aircraft engine. While test and demonstration engines have been produced, there has been no public production engine released as of 2015.
Having such an innovative idea put on hold because of the helicopters primary component is disappointing. I’m sure there is a lot of “dead weight money” balancing on those skids! Apparently there were other technical issues yet to be refined including overall weight concerns.
There is nothing unusual with these problems, and new helicopter designs usually work through them, but with no end in sight for the DeltaHawk engines public availability, it seems the Delta D2 project is on permanent hold at this time. Got some extra cash to invest???
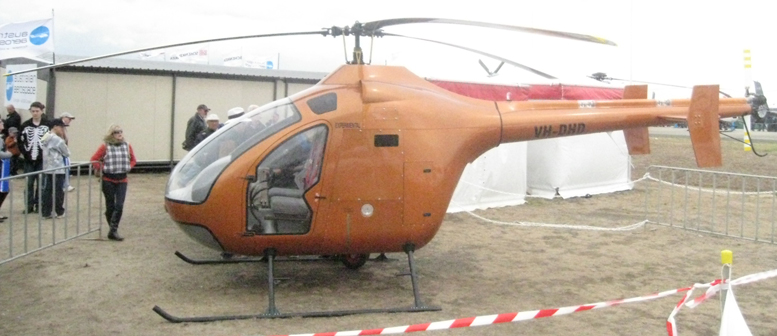
Delta helicopters Australia bio diesel helicopter
The Delta D2 Diesel Helicopter
Australia’s diesel helicopter
In an industry increasingly challenged to deal with fuel and climatic concerns, three enterprising Australians are taking a radically innovative approach. Dennis Raubenheimer investigates.
“What the….!”
Those would have been the words uttered by many people at the Australian International Airshow at Avalon in March, on first setting eyes on the Delta D2 helicopter. With an intriguing mixture of streamlined good looks (the front end) and distinctly van-like appearance (the rear) to anyone interested in helicopters the Delta was the biggest surprise at Avalon.
New helicopters do not appear every day, and to find one in one’s own national backyard, designed from the ground up by Australians, is all the more unusual. I’d have to confess to a degree of scepticism as I approached for a closer look. “Surely this can’t be an all-new development?” I thought. “A modified Schweizer 300 helicopter, maybe?” No, and no, I soon stablished.
But, while tempted to think that it may be one of those hair-raising creations built and flown by someone with a scary amount of faith in their backyard mechanical skills, a closer view revealed a level of engineering that was anything but amateurish.
But if a good look-over was not evidence enough that it was a machine to be taken seriously, a little more information would have done the trick. Not only are the Delta’s carbon-composite rotor blades fabricated by the engineer responsible for the blades fitted to several Eurocopter helicopter models, but the transmission and other major components have been designed by Bill Whitney, one of Australia’s most accomplished aeronautical engineers. And further investigation revealed yet another surprise: the Delta is the world’s first diesel-engined helicopter.
The Delta diesel helicopter is the brainchild of Graeme Smith, a Queensland entrepreneur known for importing and distributing the range of Rotorway kit-built helicopters. The Delta diesel helicopter concept originated at a time when Smith’s marketing of the Rotorway Exec helicopter in Australia, New Zealand and south-east Asia brought him into contact with people who were interested in using the machine in rural situations. One of those clients was Andrew Reid, a farmer and ex F-111 pilot who was working the Robinson R22 helicopter on vast tracts of land in northern Queensland.
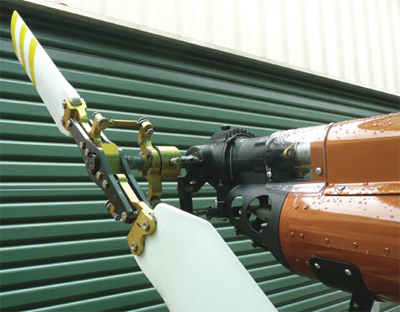
Clean tail rotor assembly with cooling fins on the tailrotor gearbox.
Reid purchased a Rotorway helicopter in the hope that it may be a more cost-effective aircraft for his farming applications. When along with its other limitations the machine proved to be underpowered, Reid and Smith discussed the possibility of replacing the Rotorway’s engine with a larger unit.
“It was the most obvious issue [with the Rotorway] that we could fix,” says Smith. “We went about finding another engine that we could put in and that I could offer to other customers who’d bought a Rotorway.”
At that stage, due to the introduction of general sales tax and a decline in the Australian dollar, the cost of importing Rotorway kits had risen so dramatically that sales of new aircraft had almost totally dried up. Recognising that the largest market still open for helicopters in Australia was in mustering, Smith saw an opportunity to offer supplementary kits that would enable the Rotorway to be used for that purpose.
Browsing the internet in search of alternative power options for the Rotorway, Smith came across a diesel engine that was rapidly gaining attention in the fixed wing sector overseas. A remarkably simple design, the Delta Hawk DH200 two-stroke V-4 was being offered as an alternative to the Lycoming and Continental 320 series motors in aircraft such as the Cessna 172. Smith and Reid immediately saw the benefits that a diesel helicopter would offer farmers in outlying areas.
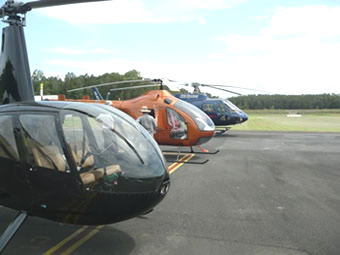
Diesel kit helicopter stands out in the line-up: R44 Delta-helicopter Gazelle Aerospatiale AS-350
“People out there understand diesel. They’ve got plenty of it. They’ve got huge tanks of it, and they know how to handle it,” says Smith. On a subsequent business trip to the US, Reid held discussions with Delta Hawk and bought one of their engines.
Though he is a fitter and turner by trade and describes himself as “pretty good” with his hands, to convert a Rotorway to the diesel engine Smith decided that they would need the services of a qualified aeronautical engineer.
A natural choice was Bill Whitney, who with 14 full aircraft designs under his belt and, fresh from having developed and certified the Boomerang trainer, also had extensive experience in certification. In addition, Whitney had worked on autogiros and had employed planetary reduction gearboxes in his design of the Vickers Vimy replica aircraft – mechanical experience that was directly relevant to helicopters.
“People out there understand diesel. They’ve got plenty of it. They’ve got huge tanks of it, and they know how to handle it.” – Graeme Smith on diesel fuel in the outback.
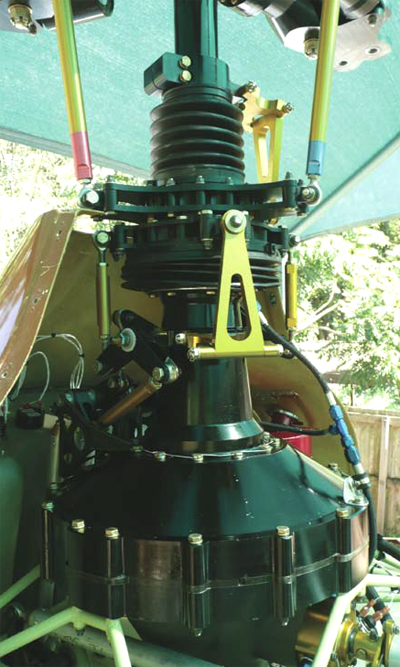
Gearbox transmission controls Delta helicopter: The standard of engineering in the Delta helicopter needs to be seen to be appreciated.
“We approached him and asked if he’d work with us and ultimately be part of the company,” says Smith. “And he said, yep he’d do that – he would design the mounting of the Delta Hawk into a Rotorway helicopter frame, as well as the gearbox and all the other ancillary bits and pieces, so that we could test the engine.”
The conversion of a Rotorway helicopter to diesel was completed and ground tested, but the team ultimately concluded that the Delta Hawk would not be a viable power plant for a do-it-yourself upgrade kit.
“It took all of my engineering know-how to be able to do it,” says Smith. “A lot of tooling and welding and a bunch of things that I have access to – but most people don’t. So the idea of selling it to somebody else as a kit was pretty much stymied from a physical point of view.”
But one other aspect of the diesel engine that made it unsuitable for the Rotorway had come as something of a surprise: the unexpectedly high power output of the diesel engine.
“We couldn’t guarantee that the Rotorway drive system – or the rotor head and blades – could take it,” explains Smith. “It was well and truly above the [original] engine that they had in the aircraft. We decided it wouldn’t be a safe or prudent thing to do. But we were so impressed with the DeltaHawk diesel engine we said to Bill, ‘Let’s build an aircraft around the engine…’.”
Funded by Andrew Reid, with Smith and Whitney contributing time on an unpaid basis, the project began with a complete reappraisal of the objectives. By then fully cognisant of the engine’s capabilities, the team set about exploring the potential for a two seat diesel helicopter to satisfy the needs of the farming and mustering market. Six years on, having been developed with the intention of initially offering it as a kit-built aircraft, the prototype approaches its first fully functional ground and hovering tests.
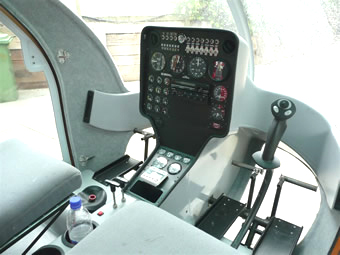
Diesel kit helicopter instrument panel.
Looking it over, for an aircraft that has yet to undergo its first test flight, the machine appears to have progressed surprisingly far. Where one may expect an experimental helicopter to be stripped down and uncomplicated before proving its basic flight capabilities, this is not the case with this machine.
Detail goes all the way down to cup holders and the most minor conveniences. And yet, it’s these sorts of details that were part of the conceptual starting point for the Delta diesel helicopter – and with weight being the primary consideration, as it is with all helicopters, it seems sensible to have worked them in from the start.
“One of the things that I wanted was to present an aircraft that was pilot friendly,” says Smith. “When I was learning to fly, I got introduced to the [daily] and preflight walk-around and found that with the Robbie there are a number of places where you had to undo covers and look into things. I wondered if I couldn’t make that easier. I’ve got inspection openings, and in places along the boom there are clear transparencies. I thought if I can make it easier for the pilot to do, he or she is more than likely going to do it. That’s my simple theory.”
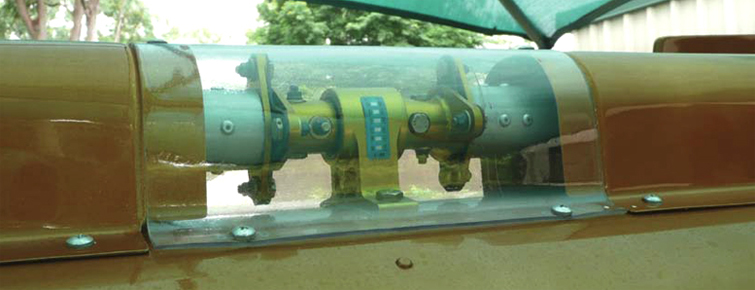
Clear inspection ports diesel helicopter
For Smith and Whitney, that goal and philosophy must have resulted in some Eureka moments. No need to dip fuel tanks – with attendant hazards like getting dirt into the fuel – when the level can be seen within each of the machine’s two semi-transparent plastic tanks through viewing slots on each side of the aircraft. And don’t get fussed about where to put your water bottle on those long hot flights through the outback; there are bottle holders conveniently placed between the seats – just where you’d expect to find them.
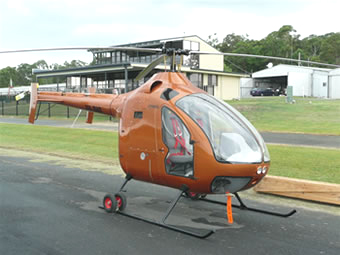
Delta diesel helicopter front view
“Where do you put your sunglasses after you jump out of the aircraft? Where do you put your phone?,” poses Smith. “These are things that everybody carries nowadays, but where do you put them? They’re only small, but they’re the sorts of things [we thought about].” To a farmer mending fences in the outback, perhaps the most outstanding feature of the Delta D2 helicopter will be its 1250 by 300 by 600-millimetre full-width cargo box, located almost directly under the rotor mast for minimal effect on the centre of gravity.
But while utility and conveniences were seen as providing a marketing advantage in the team’s target area of heli-mustering and farming, they needed a serious engineering platform on which to base it all. It was in this area that Bill Whitney’s involvement strongly influenced the project: “Bill is adamant that even though the aircraft is initially going to be offered as an amateur build experimental aircraft, he wants to design it to [a commercial standard]. As he already has a number of certified aircraft under his belt he’s very familiar with those standards. He’s stressed the whole thing [accordingly] and the paperwork is very serious.”
“You can put one end on a bit of wood and the other end on another bit of wood and stand on the middle and you can’t get them to deflect. That’s how strong they are. And they’re as light as…” – Graeme Smith on the technology in the Delta’s tail rotor blades.
Whitney confirms this standpoint, speaking freely of the challenge of designing a helicopter by comparison to a fixed-wing aircraft. It’s clear that the design choices that were made early in the program were not made from the point of view of making his life easy.
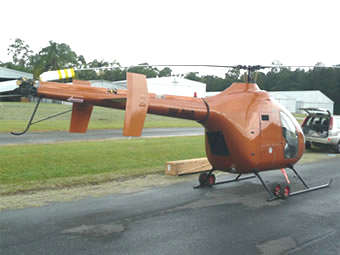
Delta diesel kit helicopter high tail boom.
While he has previously been involved in aspects of helicopter design and has worked on an autogiro project, the Delta diesel helicopter is the first full helicopter design in which he has been involved.
“It’s very new for me and I’m on a pretty steep learning curve,” he says, before giving the reasoning behind the fundamental design and explaining that a more complicated three-bladed system was chosen for safety reasons.
“We didn’t want to do a two-bladed teetering system,” says Whitney. “With teetering systems you have this zero-G loss of control problem [with potential for] mast bumping or the blades swinging down to cut the back off the aircraft.
Having an articulated system you can go down into negative G. Not that you would do that deliberately, but it gives you an extra margin for safety.”
All photos courtesy: Delta Helicopters unless otherwise specified.
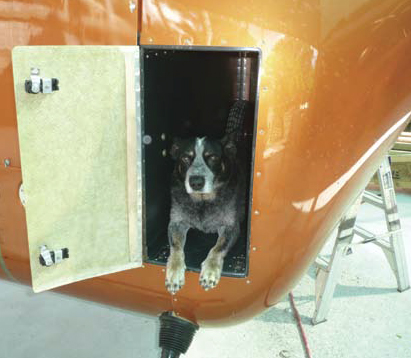
Diesel Delta helicopter cargo hatch: Delta Diesel helicopter exhibits well thought out cargo carrying ability. A helicopter with seriously useful cargo space for farmers.
But while a three-bladed, fully articulated rotor system may offer better safety in flight – it presents significant challenges to the designer. One of these is the propensity for ground resonance – a condition that can occur when blade spacing becomes asymmetric, causing oscillating forces to be thrown back and forth between the rotor system and the undercarriage. If unchecked, the condition can escalate rapidly to the point of self-destruction. The team awaits the first ground run with some understandable trepidation.
“We’re just coming up to our first ground run now, so we’ve very much got our fingers crossed concerning that,” says Whitney. He then provides an insight into how the issue of ground resonance is managed in the design. “When you look at the equations for ground resonance, you’ve got to have damping in two locations.
You’ve got to have damping in the helicopters rotor head and you’ve got to have damping in the undercarriage. And you’ve got to get the natural frequency of the aircraft on its undercarriage as low as you possibly can.” It’s around the rotor system and blades that the Delta helicopter most clearly shows professionalism. Having made a choice fairly early on that fully composite, carbon rotor blades were the way to go, the team first tried to find a local company that was able to produce them.
“We did a lot of research to try and find a way to build the helicopter rotor blades in Australia, but there was just nobody in Australia that knows anything about them,” says Smith. “No one has done it. There are plenty of people who think they can do it, but when you start pressing them they just don’t know. So I made some contacts with some people overseas that were advertising composite blades.”
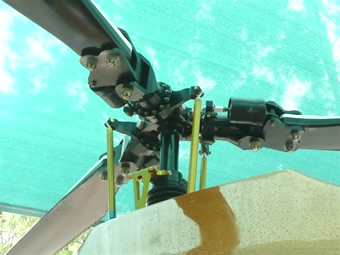
Delta helicopter articulated rotor head
The search for a blade manufacturer ended in Paris where the team located a design engineer who had previously worked for Eurocopter. Having just come out of a post-retirement competitive restriction period the engineer was keen to become involved.
By then, Bill Whitney’s son Eric had also become involved in the helicopter project and had calculated the parameters for the blades, including their basic shape and performance data.
“We were able to give that information to the guy over in Paris and he tweaked it with his experience to maximise the performance,” says Smith.
The move to have the main rotor blades made in France was one of considerable faith, and definitely did not come cheaply. In order for the development of tooling to be viable for the manufacturer, the team needed to order and prepay for 24 sets of blades.
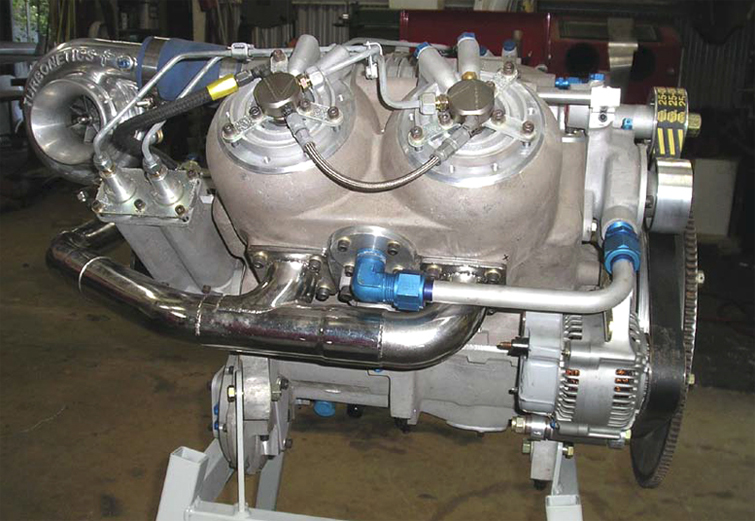
Two stroke Deltahawk diesel helicopter engine: The Delta Hawk two cycle diesel DH200 V4 engine lies at the heart of the D2 helicopter project.
“We had to pay for a lot of rotorblades that we are still yet to receive, to allow him to fund the building of the mould,” says Smith.
It may be a kit-built aircraft, but the Delta’s rotor blades use cutting edge technology. Designed for an unlimited life (or replacement depending on condition) the blades are internally lead-weighted and employ a variable chord with progressive twist – features normally found only in far more expensive or military helicopters.
“We expect to see a far more efficient blade than the common helicopter,” says Smith. “Though that technology is not new it’s not usually used in [this class of] helicopter.” The Delta’s tail rotor blades take a similarly hightechnology approach and will also be provided by the French manufacturer.
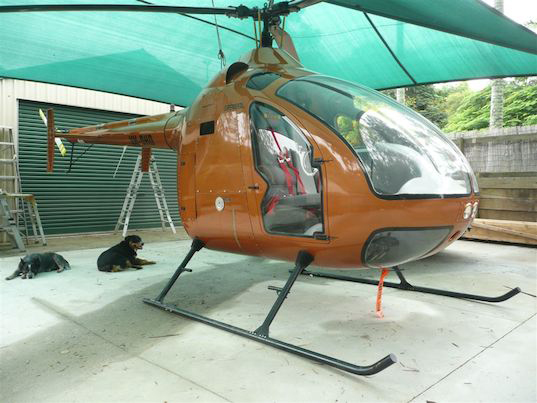
Delta D2 diesel helicopter
“They are all carbon fibre,” says Smith. “You can put one end on a bit of wood and the other end on another bit of wood and stand on the middle and you can’t get them to deflect. That’s how strong they are. And they’re as light as. There is incredible skill in knowing how to build them.”
Working our way from the main rotor system down to the engine, there are more surprises. Unlike the R22, R44 and Schweizer 300 helicopters, which each use a horizontally mounted engine connected via a multi-v-belt/clutch arrangement, the Delta diesel helicopter uses a vertically mounted engine driving a planetary gearbox through a centrifugal clutch. This gives its transmission more in common with a Bell 47 than most popular light helicopters in its class. While heavier and more complex, in the Delta Whitney has aimed for better economy through mechanical efficiency.
“The power loss through a planetary system with straight cut teeth is very small, probably less than one percent,” says Whitney. “Whereas if you use, say, spiral bevel gears or something like that you’re probably going to lose 2.5 to three percent of your power. That can be as much as six horsepower going to heating oil in the gearbox.”
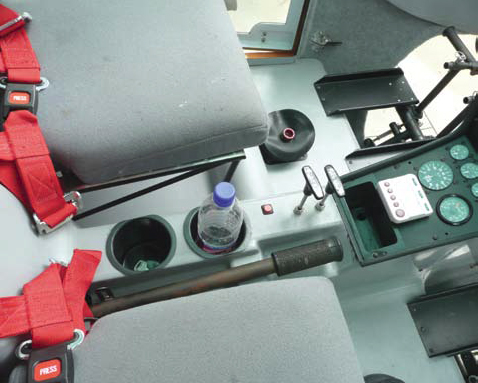
Delta diesel DH200 helicopter cockpit and collective control.
In making these choices of weight versus efficiency, the team has placed considerable faith in the power output of the four-cylinder, two-stroke, water-cooled, turbocharged diesel engine.
At the heart of this unique aircraft, the engine is central to the value they foresee in the project.
“Using a two-stroke allowed them to build a [monoblock] engine where there are no separate barrels; they’re all part of the one block,” explains Smith. “There’s no separate head and the two-stroke allowed them to get the power at a weight that is comparable to what’s out there now.
It’s not cheaper to buy the engine, but over 2000 hours you’ll save the cost of your engine in fuel and maintenance. No spark plugs to change, no magnetos to overhaul. No high tension leads, no valves and no head gaskets. There are very few parts that you need to look at from a maintenance point of view.”
Putting out a new aircraft while proving an unusually large number of unique features would appear to be risky from a financial point of view, but Smith is unrepentant. “If we are going to be successful in this we had to be better than what’s out there currently, otherwise why would people change?,” he asks. “Price is one thing, but there have got to be other things. We went about in our design to address all of the issues that the R22 helicopter has, and be better. We’ve got a cargo box; we’re running on diesel, which is available anywhere. We don’t have any belts in the system, we’re going to be faster, we’re going to be cheaper to buy and cheaper to maintain. And we’re going to use less fuel.”
“We’re just coming up to our first ground run now, so we’ve very much got our fingers crossed concerning that.” – Bill Whitney on the challenge of designing to avoid ground resonance

Delta helicopter main transmission.
Whitney supports this view and outlines the way he sees the development progressing to the next stage. “This is very much a developmental prototype,” he says. “We’re going to learn a lot of lessons and we will undoubtedly make changes in our production aircraft. The first aircraft is a bit on the heavy side (still currently an issue 2015). They always are.
We’re looking at making the undercarriage arches out of composites and changing the base structure, and we’ll probably make the main planet carrier for the transmission out of titanium rather than steel. We’d like to lose about 60 kilograms if we can. That could be a fairly big ask, but that’s what we’d like to do.”
As this article goes to press (May 2009) the Delta Helicopter team will be putting the D2 diesel helicopter through the first phases of flight-testing. Who the test pilot will be they are not saying at this stage, but do confirm that the person who will first fly the Delta will be a trained test pilot with a military background. The flight test regime will follow a textbook method for helicopters.
“We’ll progressively go through the flight test procedures establishing as we go what’s normal and then start to push the envelope once we’re comfortable with the recovery techniques in the various situations,” says Smith. “It’s not a risk free project by any means,” says Whitney. “[But our funding partner] wants to experiment and see how it goes. In life you never know until you try, do you?” HN – (HeliNews).
looks good will keep an eye out very practical.