What Does Your Aircraft Run On?
It’s dinosaur time for leaded fuels. Will avgas follow? Here’s a broad look at aviation fuel, its past and probable future.
ARTICLE DATE: January 1992
Editor’s Note: “In 1996, the U.S. Environmental Protection Agency will ban the use of leaded fuels in motor vehicles as part of the Clean Air Act Amendments of 1990.”
“Through the efforts of the Aircraft Owners and Pilots Association (AOPA), FAA, the Experimental Aircraft Association and other aviation groups, the EPA clarified that a 1992 ban on the manufacture of lead fuel burning engines does not apply to aircraft. The EPA ruling gives the general aviation community more time to develop a new aviation gasoline that is environmentally compatible.”
“Although fuel companies are currently developing alternative lead-free fuels, the problems of testing, distribution and possibly modifying engines is expected to extend well beyond the next review to occur in 1996.”
“In the meantime, avgas is still legal and available and may or may not be banned. We asked a representative of Phillips 66, the leading supplier of avgas in the United States, to comment on avgas and its possible alternatives. Jack Hammond, Phillips 66 aviation sales manager, is also on the Board of Visitors for the AOPA Flight Safety Foundation.”
The decreasing number of major players in the aviation gasoline (avgas) market has caused fears that the leaded gasoline product will no longer be available, or will be a lower quality product. The reality is actually quite to the contrary. For instance, Phillips 66, the leading supplier of avgas in the United States, has announced its intention to continue to make avgas available.
Today’s Refining Process
Avgas is the most complex fuel produced in a refinery. All avgas must meet official specifications developed through cooperative efforts between engine manufacturers, airline operators, fuel suppliers and appropriate government departments.
For this reason, strict process control is required to ensure that the stringent specifications for volatility, calorific value and anti-knock ratings are met. Like all gasolines, avgas is made from crude oil that is separated by boiling.
The high boiling point components in crude oil are used to make things such as asphalt; the middle boiling point portion is used for lubricants and oil products; and the low boiling point is used for gasolines.
When the low boiling point material is separated further and purified, the result is a liquid product that meets avgas requirements. After the addition of an additive package, the resulting liquid product is avgas.
The largest component of avgas is isooctane produced in the alkylation process. Volatility requirements for the final blend are met by the addition of isopentane. Sulfur and oxygen-containing impurities are strictly limited and only approved additives are permitted.
Due to the international nature of aviation activities, the basic technical requirements of all Western avgas producers are virtually identical and only minor differences exist in other countries.
All avgas is refined to common criteria—the American Society for Testing and Materials (ASTM) specification, which contains sections covering materials, workmanship, and chemical and physical requirements.
Anti-Knock Test
Fuel grades are classified by their anti-knock quality characteristics as determined in single-cylinder laboratory engines. Knocking in an engine is caused—usually under either excessive load or excessive temperature—when the air/fuel charge ignites spontaneously.
Premature detonation can damage an engine if allowed to persist and can limit the amount of power available from the aircraft engine, hence the reason for the addition of anti-knock compounds to fuel.
Fuel grades are determined by their ability to provide knock-free operation as compared to reference or “bench-mark” blends of pure and leaded isooctane and n-heptane. The rating of such fuel is expressed as a performance number as compared with leaded isooctane.
Pure isooctane has an anti-knock rating of 100, therefore, 100 octane avgas means the sample fuel matches the anti-knock performance of pure isooctane.
ASTM specifications designate aviation gasoline grades with two numbers, i.e.: 100/130. The lower number denotes an anit-knock of 100 while running with a lean fuel/air mixture. The 130 rating is determined under rich mixture,full power conditions. The double rating system for anti-knock is currently being phased out.
Volatility Testing
All liquid fuels must be easily convertible from storage in liquid form to vapor in the engine to allow formation of the combustible air/fuel mixture. If fuel volatility (boiling point) is too low, liquid fuel is introduced into the cylinder and washes lubricant from the cylinders, diluting the crankcase oil. Also, performance will be reduced.
Conversely, if volatility is too high, fuel can vaporize in the tank and fuel lines causing undue venting losses and the possibility of fuel starvation through “vapor lock.” The cooling effect due to rapid vaporization of excessive amounts of high volatile material can also cause ice formation in the carburetor under certain conditions of humidity and air temperature.
The boiling characteristic of avgas is determined by a distillation test where a sample of fuel is heated and the vapor temperature is recorded for the percentages of evaporation throughout the temperature range.
All spark-ignition engine fuels have a vapor pressure that is a measure of the tendency of the more volatile fuel components to escape from the fuel tank in the form of vapor. When an aircraft climbs rapidly to a high altitude, the atmospheric pressure over the fuel is reduced and may become less than the vapor pressure of the fuel at its prevailing temperature.
If this occurs, the fuel will “boil,” and considerable quantities of the more volatile components will escape as vapor through the tank vents. Similar vapor generation in fuel lines and carburetors can result in stoppage of fuel flow to the engine, causing engine shutdown. Vapor pressure limits for avgas are between 5.5 to 7 psi.
The lower limit of 5.5 psi is necessary for engine starting; the 7 psi limit controls excessive vapor formation during high altitude flight and during “weathering” losses while the aircraft is in storage.
The Future Of Leaded Avgas
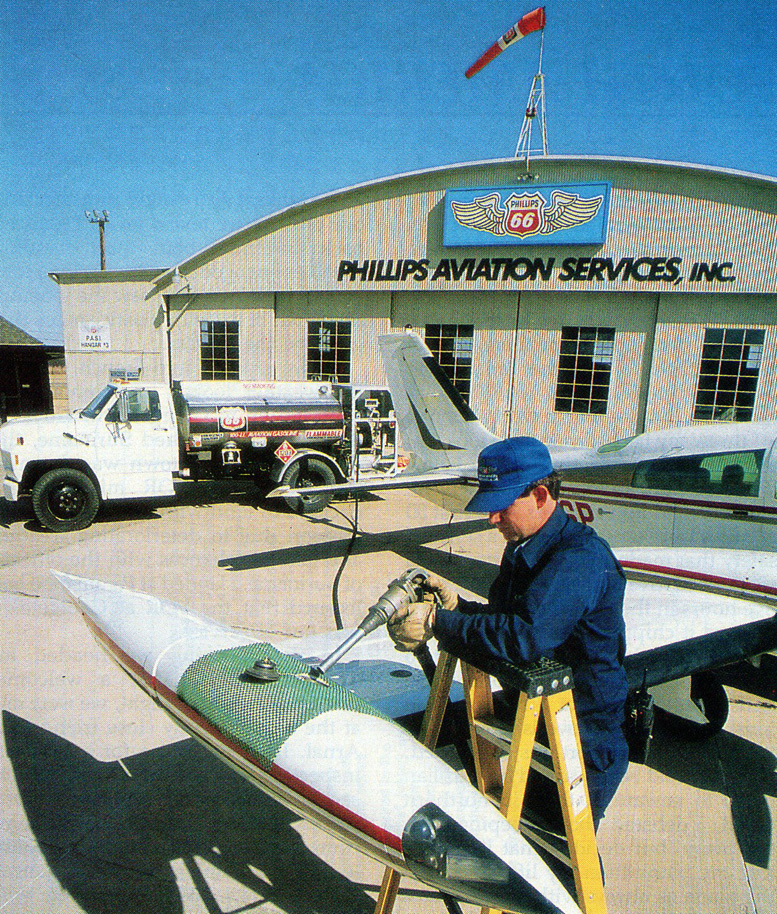
A line crew member fills a Cessna 310R with avgas at Phillips 66 FBO. Clean facilities and fueling equipment, knowledgeable line personnel and a branded product are signs that an FBO has quality avgas.
No effective and practical replacement has been found for tetraethyl lead in aviation piston engine fuel that will deliver the performance needed for efficient and safe engine operation. So at least for the near future, leaded fuels will continue to be used in general aviation.
Major suppliers such as Phillips 66 will continue their aviation fuel distribution systems as suppliers less committed to general aviation leave the market. The ability to stay in the avgas business in the future is going to require some major changes in the distribution system.
As the need for leaded fuels in the automotive market continues to dwindle, it will be more difficult to distribute leaded products such as avgas through common carrier pipelines or tankers. Therefore, pilots may see more suppliers dropping out of the market.
The History Of Avgas
Early on, it was discovered that a special quality that aviation fuel must have was a lower vapor pressure than auto fuel. By the end of World War I, Phillips Petroleum Co. had pioneered a distillation process to reduce the vapor pressure of gasoline so it could be used in aircraft.
The next quantum leap in technology occurred in the 1920s when it was discovered that the addition of tetraethyl lead (TEL) increased the fuel’s octane rating and controlled detonation and pre-ignition in the combustion chamber.
This discovery was particularly significant to aviation because of the high altitude, power and heat environments in which aircraft engines operate.
Polymerization, a refining technique that combined high volatility components in molecular form to produce more powerful, smoother-burning fuels, was developed in 1935. The development was the forerunner of 100-octane aviation fuel.
During the early years of World War II, commercial production of alkylate, an important component of high octane aviation gasoline, boosted fuel ratings to as high as 145 octane. The Phillips 66 process, which used hydrofluoric acid as a catalyst was hailed as the industry’s most important wartime contribution.
In 1944, the company began producing diisopropyl, a fuel ingredient that gave military airplanes a super fuel for more power. In the ensuing years, the necessity of using specialized higher octane fuels gradually diminished as lower-powered, simpler engines became the standard in civil aviation.
In the 1970s, however, concern over the environmental impact of using leaded gasoline and the subsequent elimination of TEL in auto fuel predicated the introduction of 100 Low Lead as the sole grade widely available to general aviation.
Mogas: Is Auto Gas A Viable Alternative?
While supplemental type certificates have been issued to allow the use of automotive or motor gasoline in certain models of aircraft, most aviation piston engine manufacturers specifically exclude motor gasoline from their list of approved fuels. In addition, many fuel refiners disapprove of the use of auto fuel in aircraft.
The primary reason is that motor gasoline has a wider range of applications and subsequently more tolerant specifications. It can vary in composition and quality from supplier to supplier, from country to country, and from season to season.
It is not a closely or uniformly specified product and a growing variable in recent years is the increasing inclusion of strong detergent additives, alcohols and other oxygenates in its composition.
Aircraft that have been approved to use “mogas” have been permitted to do so because of design features that make them less sensitive to variable fuel properties.
The responsibility for using automotive gasoline still rests with the owner/operator, the parties that have received the approval, and regulatory agencies that approved its use. Another reason mogas is risky is that octane requirements designed into modern aircraft engines cannot be reached with conventional unleaded motor gasolines.
Before using mogas in your aircraft, review and consider the following:
-
Mogas has a wider distillation range than avgas, which could promote poor distribution of anti-knock compounds in some carbureted engines.
-
Higher volatility and vapor pressure of mogas could overtax the vapor handling capabilities of certain aircraft and could lead to vapor lock, carburetor icing, or fire.
-
Mogas has a shorter storage life than avgas and can form gum deposits.
-
Due to higher aromatics content and the possible presence of oxygenates, mogas could have solvent characteristics unsuitable for some aircraft. Seals, gaskets, flexible fuel lines and some fuel tank materials could be affected.
-
Mogas may contain additives that could prove incompatible with certain engine or airframe components.
Specifically, additives designed to remove fuel injector and valve deposits in car engines may have the opposite effect in an aircraft engine.
-
Mogas testing and quality protection measures are less stringent that for avgas, resulting in a greater possibility of contamination occurring and less possibility of detection.
-
The absence of anti-knock compounds in unleaded mogas means prevention of excessive valve seat wear in certain engines is not provided.
Common Myths About Aviation Oil
Myth: Oil is oil and most brands are pretty much the same.
All aviation oils provide some form of lubrication, but that’s where similarities end. Each refiner blends proprietary additives to enhance the oil and provide predictable performance characteristics.
Using the wrong oil can lead to possible lubrication related engine failures. Using the right aviation oil can help improve engine efficiency and extend engine life.
Myth: You can use automotive oil in an airplane engine.
The most important reason you can’t use automotive oil in an aircraft engine is because there are a large number of additives in automotive oil that are designed for use in water-cooled engines operating within a certain range of temperatures and pressures and at constantly changing levels of power.
Aircraft engines are air cooled and operate in a much wider range of parameters.
Myth: Oil viscosity does not matter.
Viscosity plays the key role in preventing engine wear and is also important at low temperatures for pump-ability.
Viscosity determines how easy it is for oil to be picked up by the oil pump and moved through lines and passages.
You need to have an oil thick enough to keep moving parts from contacting, and thin enough to permit adequate flow and minimize viscous drag.
Myth: Oil never wears out.
Technically, the oil does not wear out, however, extended use causes the oil’s additivies to wear out or become depleted. The best example of how additives are used up is an oil’s suspension quality. Aviation oil is designed to suspend dirt and metal particles picked up from your engine.
Eventually the oil will become “over-suspended.” The principal reason oil is changed at regular intervals is to rid the engine of these suspended impurities.
Old oil with a high degree of contaminants bombard engine components and may lead to bearing corrosion and deposit buildup.
In addition, overworked oil can get to the point where it will not suspend the additional particles created during engine operation. This produces particle buildup or sludge.
Overworked oil will result in similar depletion of the oil’s other additives. The result is the oil will no longer be performing the benefits the additives were designed to provide.
Myth: Oil removed during an oil change should appear clean.
If an oil is doing its job properly, it should suspend dirt, metallic wear materials and unburned carbon. Therefore, when you changed your oil it should appear dirty.
Myth: Fuel-injected engines do not need a multi-viscosity oil.
Proponents of fuel-injected engines claim they start better in cold weather that a carbureted engine. For this reason, a multi-viscosity oil is more important in a fuel-injected engine.
Single-viscosity oils may not flow quickly enough to provide adequate lubrication at the low temperatures a fuel-injected engine can start up at.
The single-viscosity oil becomes too sluggish at these cold temperatures, creating excessive viscous drag. Remember that approximately 85 percent of bearing wear occurs during the start up phase.
Myth: A cold start is anything below freezing.
An engine is designed to provide power while it’s running and engineered to run best at warm operating temperatures. So, judged by how the engine sees it, a cold start is anything below 60 degrees F.
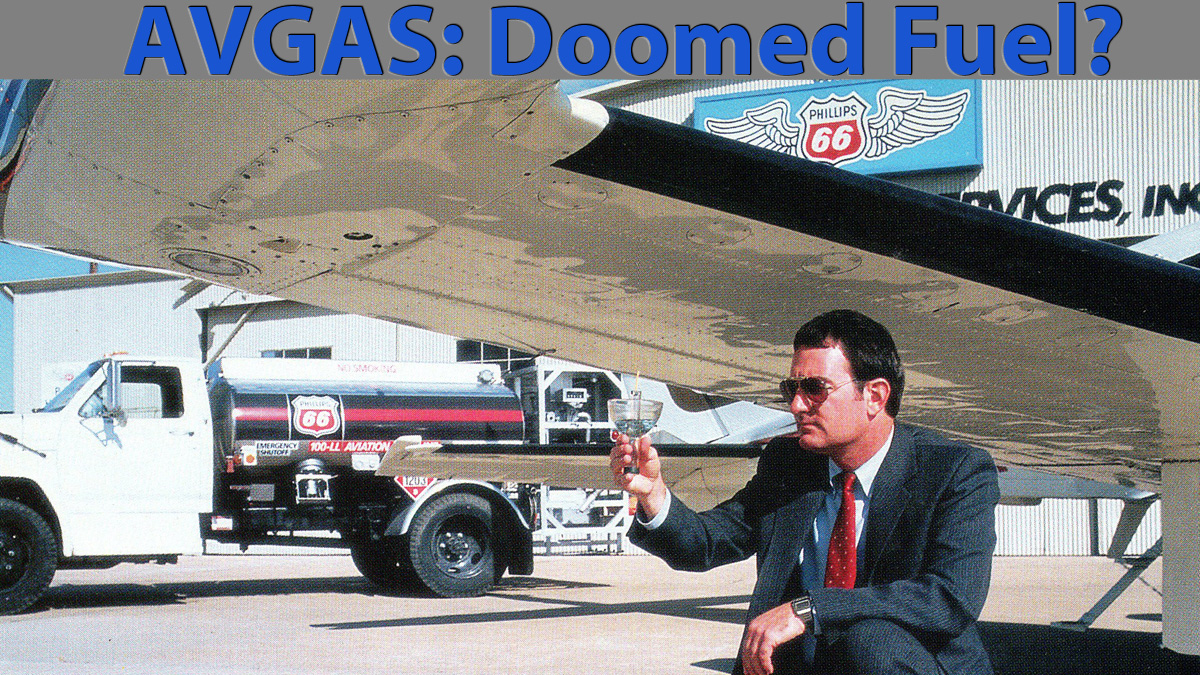
Be the first to comment on "Is AVGAS A Doomed Fuel?"