Reprint with permission from US Aviator Magazine (Volume 6 – Issue 12 – December 1994) for Australian Mini Copters
Anyone Got A Good Recipe For Crow?
Sometimes you get to eat the bear; sometimes the bear eats you… and that also applies to crow… of which I am about to consume copious amounts. I’ve been after Revolution Helicopter for the better part of four years to get their single-place Mini 500 helicopter done and let me fly it. And now I’ve done it.
It has been over four years since Dennis Fetters bailed out of the gyroplane market, sold Air Command, and announced that he was gonna build the ultimate sport helicopter. Initially, we wished him well and waited expectantly… and waited… and waited… and waited. And then… we waited some more.
In the meantime, serious-and some not-so-serious-competition arose: the Elisport Angel, the Nolan PC, the Ultrasport 254, the Lonestar, and other small sport helicopters popped up and threatened to steal Fetter’s thunder as they produced real, live helicopters (some already up and flying; some not).
In these years, our patience turned into impatience as we continued to wait for the Mini-500 to get done, get in the air, and be made available to us so we could find out if it flew worth a darn. Even after its first flight some two years ago, I expected to have to wait awhile… but as a fair amount of time passed, I really began to worry and wonder if this project was going to happen at all.
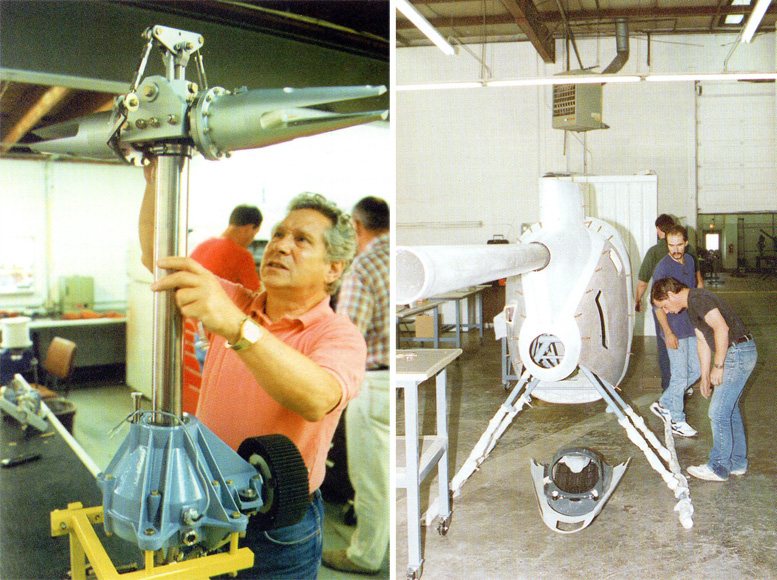
LEFT: James Hepp seen during final assembly on his transmission control assembly before its installation.
RIGHT: A Revolution worker does a conformity check on a new ship to make sure that parts and assemblies are meeting spec before full production is started.
However, the truth was that Fetters did something very uncharacteristic of his breed: he took his time , he didn’t make any significant compromises, and he tried to get “it” right. And from all our recent experiences, as well as several hours of flying, I can unabashedly tell you, at this point, it sure as heck looks like he did get “it” right.
As the third highest time Mini-500 pilot in the world (as of this writing), I’m here to tell you that the little single-place Mini-500 is a dream… and a ball to fly! So pull out your best recipes for crow (I’m kinda partial to barbecue, myself) and serve ’em up, cause the ol’ Zoomer is about to eat as much as he’s had to for quite the while. Oh well, that’s life!
Oh Yeah… Revolution’s Mini 500 Helicopter “The Aircraft!”
Enough of the apologies—onto the aircraft! The final version of the Revolution Mini-500 helicopter is a 485-lb, single-seat helicopter utilizing a single, semi-rigid, teetering, underslung main rotor and a free-teetering, rigid in-plane tail rotor.
Assuming a shape not too dissimilar from the early Hughes 500 turbine choppers, the fiberglass-shelled Mini-500 can be flown door-less or with both cockpit doors closed for higher speed operations or cooler conditions. A set of widely-spaced skids serves landing gear duty and the machine has generously proportioned vertical and horizontal stabilizers to enhance in-flight stability.
For the record, this is no ultralight and was never meant to be; Dennis is of the opinion that current technology is not capable of mass-producing a durable, single-seat helicopter that could be consistently built under the weight limit of 254 lbs.
It is also interesting to note that Revolution will not ship any of their customers a tail rotor until they have shown compliance with the factory’s recommended minimum experience limits to fly the Mini 500 helicopter.
The machine seems pretty well-built. Helicopters are, by nature, fairly unforgiving machines in a number of critical areas… and the engineering associated with them has always been extensive. The Mini-500 has also been arduously researched.
While not the recipient of a certified engineering research program, the folks at Revolution seem to have done a lot to maximize the strength and durability of this aircraft by doing something very simple: figure the very greatest loads, fatigue cycles, and stresses put upon each critical component and sub-assembly and then build something that will withstand several times that same amount. It’s a simple idea, but it can work and so far, it has.
For example, the Mini 500 helicopter rotor blades are expected to record stresses in the neighborhood of 8810 lbs at full rpm in terms of forces attempting to pull the blades out of the rotor hub–but Revolution claims that they have pull-tested their blades to over 41,000 lbs. Yes, it sounds like overkill, but that kind of overkill sounds like a good thing to me.
The Mini-500 is a cute little rascal. That smooth and racy exterior, however, is the result of several less-than-optimal attempts that finally resulted in Fetter’s choice of a pre-preg composite architecture instead of the simpler (and cheaper) “wet-layup” method previously employed. The new pre-preg fuselage shell parts are 50% lighter, 200% stronger, and twice as durable as those they replaced.
All composite components are vacuum-bagged and heat-treated to 250 degrees. The fuselage and cabin have been built in such a manner that huge sections of the aircraft can be removed or displaced for internal inspection, maintenance, or dazzling your friends with a look at its innards.
I watched the entire rear section of the Mini 500 helicopter be removed with a screwdriver in just a few minutes to allow extensive access to the engine, drivetrain, and fuel system. Pretty slick. The windshield, by the way, is vacuum-formed in-house of a shatter-resistant poly-carbonate.
Nuts and Bolts
The machine is built on a rugged 4130 chromoly-steel-welded tube structure that supports most of the major components directly. The triangulated frame is heliarc welded and shot-peened for stress relief prior to a conformity inspection.
A number of hard points have been installed to serve as the anchoring points for other major chopper systems. The frame has been designed to serve as a shock-absorbing structure and was specifically engineered for a progressive failure pattern that would tend to protect the cabin and the pilot in case of a high-speed impact.
The Mini-500 has a fairly good-sized instrument pedestal that can accommodate more than a few toys. The machine comes standard with a pretty good assortment of gadgets: altimeter, ASI, vertical speed, mag compass, slip and bank, engine/rotor tachometer, and engine coolant temperature.
Additionally, a low rotor rpm warning light is prominently affixed to the panel as well, just in case. One optional item that I greatly recommend is a set of chip detectors for the Mini 500 helicopter main and tail rotor system.
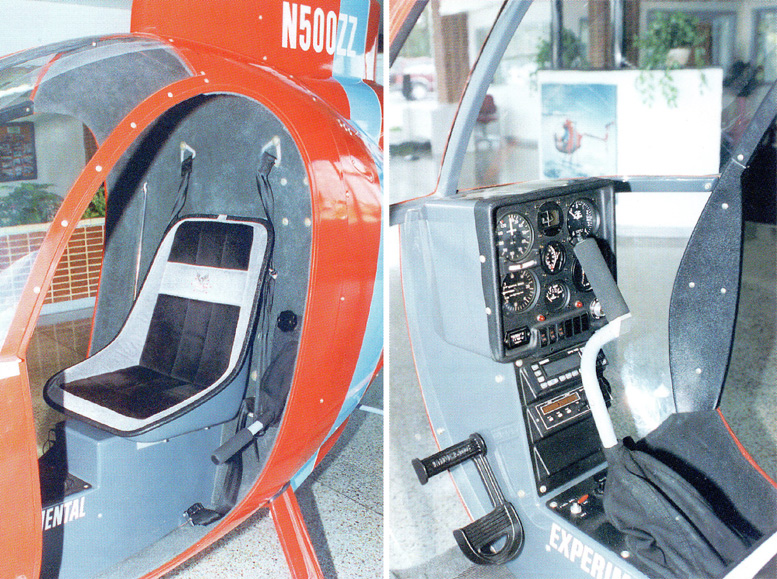
LEFT: The interior is fairly roomy and I found it to have good head and great shoulder room; it should be be able to handle big six-footers (I’m 5′ 10″).
RIGHT: I rather liked the instrument pedestal, which has plenty of room for toys and goodies, – note the great radio positioning underneath the main pedestal.
These consist of a set of lights attached electrically to some magnetic probes that will alert you when either set of transmissions starts making metal…and therefore, the possibility of impending failure. A small bank of switches on the bottom of the widest portion of the pedestal serve various chores-master, instruments, radios, lighting, etc.
Below that, there is a considerable amount of room for radios, navigation devices, even a CD player, should you so prefer. The cabin measures 34.5″ wide, 52.75″ high, and is 51″ in length. According to the factory, pilots over 6′ tall and up to 250 lbs can be accommodated.
There is a small tunnel that runs lengthwise in the center of the cabin and hides some of the cyclic control sticks’ components. At the base of the cyclic control is a small fabric boot that can be removed to offer more access to the base of the control stick and associated mechanisms.
The main rotor and its transmission assembly is the heart of this baby, and for obvious reasons, you want to take good care of it. Thankfully, this assembly looks pretty rugged. The Rotax-powered Mini-500 transmits power from the engine via a cog-type synchronous drive belt to a sprocket that is mounted on the main transmission pinion.
This sprocket also houses the sprague clutch (an over-running clutch that allows the rotor to free-wheel during power loss or significant power reduction; it also allows autorotation). Power then translates to the main transmission via a ring gear in sympathy with the pinion. A 4130 steel tube serves as the main rotor mast and turns at 546 rpm at full tilt.
The Mini 500 helicopter main transmission reportedly has a service life of 2000 hrs. The tail rotor is controlled via a set of push-pull cables that connect to the anti-torque pedals in the cockpit and a bellcrank mounted on the tail rotor gear box.
Power is conducted to the tail rotor transmission via a long aluminum drive shaft that is well-supported by a number of bearings inside the beefy, five-inch aluminum tail boom. A splined coupling mates with the drive shaft and turns the tail rotor at its max speed of 2671 rpm.
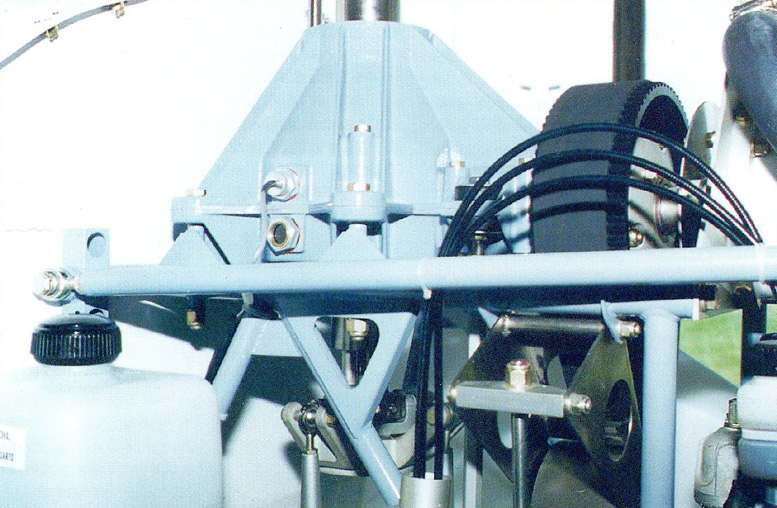
A 4130 steel tube serves as the main rotor mast and turns at 546 rpm at full tilt. The main transmission reportedly has a service life of 2000 hrs.
The rotor head is a novel design and has been the recipient of at least one US patent of which we are aware. The main difference between this rotor head and most others is the fact that there is no swash plate; cyclic pitching rotor commands are transmitted via control rods that extend through the hollow main rotor shaft.
The rotor hubs are machined from solid 6061 T6 aluminum. The spindles are likewise machined from 4130 steel. The Mini 500 helicopter rotor blades are a composite design, utilizing an extruded aluminum leading edge “D-Cell” spar that is encased inside a pre-preg epoxy fiberglass skin.
The core of the blade is machined foam. Each blade weighs 17.6 lbs and has a one-pound steel tip weight installed to increase the blades’ mass inertia. The symmetrical blades are cured with a constant, 8-degree twist and are 9′ long.
The main rotor, with a disk span of 19′. is a semi-rigid, teetering, underslung design. Disk loading at max gross is only 2.8 lbs per sq ft. The tail rotor blades are all aluminum. An aluminum spar is wrapped inside an aluminum skin which is heat-bonded with an epoxy film adhesive.
Different Strokes…
Power comes courtesy of a single, two-stroke Rotax 582 with dual CD1 ignition producing 67 hp. The excellent power-to-weight ratio of this little liquid-cooled, oil-injected engine seems to be tailor-made for this bird and this application.
There is a lot of scuttle-butt running about as to whether a two-stroke engine is capable of working dependably in a helicopter, but the fact of the matter is that the internally-mounted Rotax should enjoy a somewhat more dependable life inside the Mini 500 helicopter than outside/in direct contact with the airstream, such as it might be in a number of fixed-wing applications.
Erratic heating and cooling is a killer in two-strokes, causing poor carburetion. plug fouling, and a number of other problems; however, the temperature range inside the Mini-500 (which also has an additional six-bladed fan to cool the engine chamber, by the way) should be fairly constant, and lend itself to reliable operation.
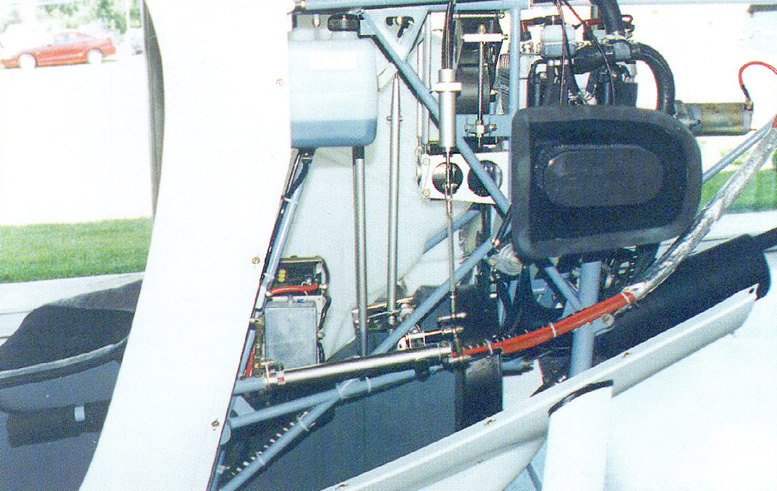
The entire fuselage segment can be removed for inspection or maintenance… and offers nearly unrestricted access to everything internal.
So far, none of the factory birds have had a lick of trouble (and during my flights I never saw more than 150-160 degrees of water temp).
This engine burns auto gas without a hiccup and the 14.7-gallon fuel capacity should offer at least three hours of normal operation. The bird has a standard electric starter which will ease starting chores quite a bit. Estimated engine TBO is 300 hrs.
The Mini-500 has a prominent horizontal stabilizer in a “T” tail configuration affixed to the top of the vertical stab and well above the tail rotor. A small skid on the underside of the vertical stab protects the tail rotor and boom from inadvertent ground strikes during quick stops or autorotation practice.
Playing It Safe
The Revolution folks are definitely playing a very conservative game with this aircraft. Despite the fact that I had several hundred rotary-winged flight hours, as well as both Commercial and CFI ratings in helicopters, I met Brian Thomas out at a nearby airport in order to demonstrate my abilities in a rented R-22 helicopter, which also became a good platform from which Brian could make control and handling comparisons so as to approximate or describe the individual characteristics of the Mini.
It was a good session and in addition to having a chance to reacquaint myself with one of my favorite flying machines, I also met pro football legend Joe Montana, who was at the flight school for a lesson-he’s pursuing an instrument rating.
….Incidentally, he’s a heck of a nice guy and seems to have a proper head on his shoulders when it comes to what he wants and expects from flight lessons. A nice meeting. I look forward to meeting him again sometime.
To any rate, Brian ran me through a number of coordination exercises in the R-22 — a few approaches and an autorotation (one of which was really bad; I was actually pretty rusty at this point, and I knew it) or two-and then indicated that I hadn’t scared him so badly that we couldn’t give the Mini-500 a try, and after a day’s wait for better winds, we did just that.
We approached the check-out process with a few major goals: take it slowly, do it safely, and no funny stuff. Brian and Dennis were both in attendance for these efforts and over the course of the next few hours, we had a ball unveiling the secrets of the little Revolution chopper.
Most appreciated was Brian’s counsel on the many small differences I could expect in flying the Mini 500 helicopter as compared to the Robinson R-22. Brian stood guard while I got settled in, gave me a few last pointers, and walked out of rotor range.
Just Me And The Mini!
Finally! Alone at last, just me and the Mini! The bird started very quickly and I allowed it to idle for a little while to get the water temp up (as well as allow me to get used to the gauges, the feelings, and turn on the radio).
I released the friction locks on both the cyclic and collective control systems and stirred them slightly to make sure that I had full freedom of motion and slowly brought the engine on line and then let the rotor pick up rpm. There were significant vibrations that were associated with rpm’s below 80%, but once over that, the system smoothes out nicely.
I was told that the upper limits of the Mini 500 helicopter rotor operating range were very generous and that slight overspeeds were not something to be worried about… but to make sure that I never let my rotor rpm decay below 90% (there is a warning light that comes on and warns you at 95%).
So I wrapped up the throttle and let the rotor rpm (unlike the little R-22, the rotor rpm is on the left side of the gauge while engine rpm is on the right) come up to 100% and then “split the needles” and quickly rolled the throttle hard clockwise to idle the engine to make sure that the sprague clutch was operating properly. A mag check showed the dual ignition system was working well, and a quick control check showed everything was still operating freely.
Not able to put off the inevitable any longer, I spooled the engine up to 100%, allowed the rotor rpm to come up slightly above the green and into the yellow (as I had been advised was the accepted procedure), and slowly raised the collective to the point where the machine felt a mite light on the skids.
I was cautioned previously most pilots in early transition flights have a tendency to over-control… and I was no exception. As I lifted off and immediately over-corrected wildly for some sideways drift, I anchored my arm against my knee to give it some additional stability.
I found the Mini 500 helicopter cyclic control stick to be mounted a bit high for my tastes, especially when I had to bring my finger up to depress the transmit switch. I found that by and large, my best hover technique came with my arm resting against my knee and holding the stick lightly with a thumb and two fingers.
Later, as I became used to the system, this was less necessary. It’s those first 30 seconds of Mini flying that are most likely to cause you trouble; after that, just hang on and let the machine do the flying.
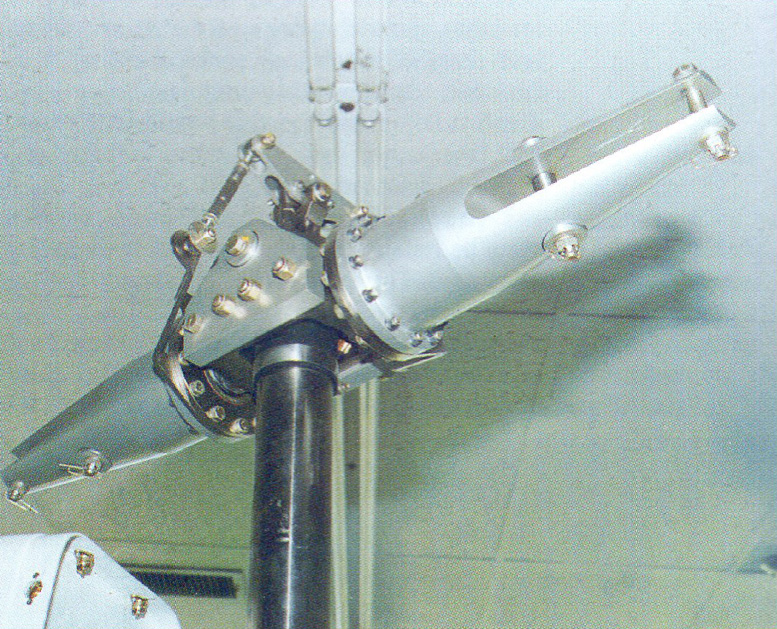
The Mini’s ingenious rotor head uses no swashplate and hides all control rods inside the main rotor shaft.
The next few minutes required a bit of patience as I lifted off, hovered briefly, and set down the better part of two dozen times while I began to understand the responsive behavior of the Mini’s cyclic control system, I was surprised to find that with an 85-degree day, a 200-lb dead weight (me), and 42 lbs of fuel, there was still several hundred engine rpm available to me for hover and lift-off.
Since the helicopter is most inefficient in hover (the machine becomes far more efficient in forward flight, especially past “translation” speeds), I was somewhat less concerned over whether the 582 had enough power to do the job (remember, the Mini was supposed to be over 100 lbs lighter than it turned out to be and several of the Doubting Thomases had pronounced that the 582 would probably not have enough power to do the job I was one of them… wrong again!).
Initial control inputs revealed light-to-moderate pressures, a slightly wide cyclic operating range, a bit of mechanical feedback (felt as a “bounce” in the stick in sympathy with the rotor system), and a very linear control response curve. The collective control has an adjustable friction setting and I pretty much let it hang loose throughout my flights.
The physical range of collective pitching action seems reasonable but I was a mite unhappy with the throttle response range—the twist grip has a wide range of actuation that occasionally required me to re position my hand to be able to get full throttle after previously handling it at normal operating ranges.
A somewhat less wide-ranging grip would seem to be in order, but not too much so. I also found the Mini 500 helicopter grip to be a bit on the tight side and would like to see slightly lighter forces required for motivation.
Throttle/collective correlation is pretty good but I did find a consistent need for some fine-tuning in hover. The Mini’s correlator is totally mechanical and may be ground adjusted by the pilot, as necessary.
The Mini 500 helicopter instrument panel was very visible throughout the flight, even when fighting with direct sunlight, but it is a bit of a far reach if you need to change a radio frequency for example.
As I attempted my initial lift-offs and landings (which bore an uncanny resemblance to the antics of a drunken sailor), the first think I did was establish the sight picture I would need in the hover to be able to ascertain what level flight and level hover was…Fixating on the ground or the cockpit is a common difficulty for new helicopter pilots or transitioning chopper jockeys and looking out to get the “picture” will help avoid uneven set-downs.
One other note: the rotor on this aircraft is mounted so high that there is, technically, no ground effect (hence the H.I.G.E. and H.O.G.E. specs are identical) so those expecting a bit of a “cushion” from ground effect are not going to find it.
The visibility in this critter is quite good, especially for tight operations where excellent peripheral viability can be a real benefit. The R-22 that I flew the day before often requires a little “stick-stirring” to keep things level on lift-off…but this will get you into trouble in the Mini…which wants you very much to leave well enough alone (kind of like a Hughes 269 helicopter).
The tendency to over-control needs to be resisted at all costs; that is the secret to the Mini. Take your time, make small corrections, and you’ll have a ball… go chasing every bit of drift and you’ll be all over God’s green earth in no time.
The Mini responds well to the collective lever. As long as you make sure that you keep the engine rpm in the “high green” on the tachometer, there shouldn’t be any difficulty, even in fairly sudden liftoffs, although I found it best to heed Brian’s advice to pull on a little too much throttle and let it settle as the rotor bit in and we flew.
I spent the first hour just playing with the hover and getting a feel for the cyclic.
Once one controls the urge to overcontrol, the bird pretty much does fine all by itself. Pedal turns came easily, although as the wind started coming up, I became aware of a pronounced weathervaning tendency (but the anti-torque controls in this thing are formidable and counter everything handily).
I appreciate the redesign that Dennis subjected the anti-torque pedals to… there is now a lip at the bottom that cups the bottom of the foot well and eliminates slip-sliding in bouncy conditions. Anti-torque response is awesome and once one gains some proficiency with the beast, you can do some vicious pedal turns that will give you whiplash if you don’t tense your neck muscles. FUN!
Before I Get Too Much Farther Into The Flight Dynamics Of This Machine. Let’s Pause For A Brief Intermission…
It seems to me that a quick primer on helicopter operation might be in order for those of you who have not yet had the pleasure (and pain) of learning to fly one. There are three primary control systems in the average chopper.
The main control stick (mounted in front of the seat) is called the cyclic pitch control and handles the equivalent of pitch and roll while the “rudder pedals” that sit in front of the pilot are actually called “anti-torque pedals” and yaw the helicopter much like they would in an aircraft.
The anti-torque pedals control the tail rotor… the small set of blades that sit on the back of the chopper and counter-act the torque effect of the main rotor. Without them, the machine would spin like a top opposite the main rotor’s direction of rotation. The long control stick on the left of the pilot is the collective pitch control system.
It has a twist grip on the end that controls engine rpm (twisting counter-clockwise/toward the outside of the cabin), while raising or lowering the stick itself changes the pitch angle of the Mini 500 helicopter rotor blades (UP if you want to do likewise, down for same…).
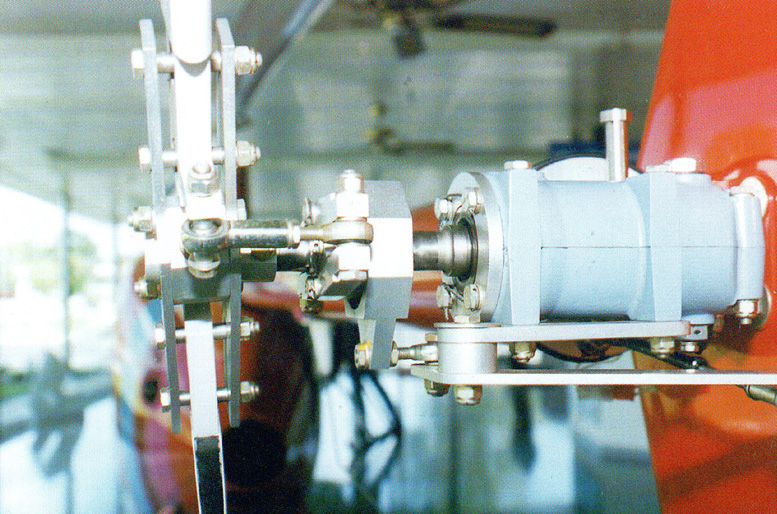
The tail rotor and gear box assembly. Pretty rugged-looking little devil, isn’t it?
A mechanical mixing system correlates throttle and collective pitch movement somewhat so that as you raise the collective, the throttle will increase a proportionate amount while fine adjustments may be made through the twist grip.
The throttle can be decoupled from the collective pitch system simply by twisting the throttle closed in order to idle the engine quickly on the ground or simulate power-off characteristics in flight to practice autorotations. The real trick comes in maintaining the appropriate attitudes while making sure that the engine and rotor rpm are being kept within proper limits.
The whole system has been likened to balancing a marble on top of a beach ball and at times, that comparison seems somewhat apt. It is not a hard skill to learn, but it is not learned quickly; most flight students take all of the minimum recommended course times (and often a fair amount more) in pursuit of a chopper license.
Look Out Below!
What to watch out for? Obviously, engine failure is the big nasty gremlin, but contrary to some popular rumors, helicopters glide pretty well (although the sink rate is usually pretty high) and can even be safer to land, without power, than many airplanes, due to the lessened landing requirements, space-wise, at point of touch down.
The process of landing an unpowered helicopter is called “autorotation” and can be something of a delicate balancing act, at times, depending upon the properties of the individual helicopter.
The key to a proper autorotation (‘scuse the oversimplification, fellow chopper pilots, but this article has to be kept under 7000 words and I think I’ve already blown past that) is to “store” the energy left in the free-wheeling rotor by lessening the collective pitch, maintaining an efficient glide speed (thereby lowering induced drag), and saving that rpm for the landing where one will both slow the aircraft by using aft cyclic pitch (which will tend to “load” the rotor somewhat and add additional rpm to the program) and then bringing in the collective pitch control to increase the blades’ angle of attack, slow the descent, and thereby make a soft landing.
The big rule in autorotations is that “rpm is life”. Have a lot of rotor rpm at the point of touchdown and you’ll generally walk away from the scenario; but get sloppy and you not only get to buy the farm, you’ll probably plow a fair part of it before everything comes to a complete stop.
The biggest screw-ups occur to those who let the rotor rpm decay to unsafe levels (which can often result in catastrophic rotor failure on many semi-rigid rotor systems) and fail to properly arrest the descent rate prior to impact—or who simply select a bad landing area. Another rotor emergency possibility includes the loss of tail rotor control through drive failure or blade separation.
If you are in a cruise or near-cruise configuration, the job is not as bad as it sounds, as most machines have a fair amount of directional stability due to stabilizing fins, fuselage design, and the like. However, the slower you are. the less likely you are to maintain control while under power.
Under many conditions, it is possible to continue flying, usually under reduced power, for a short time in order to find a hospitable landing area but an autorotation landing, usually a run-on (something like an airplane landing… with residual forward speed absorbed by the skids) is often necessary.
One of the biggest problems one must avoid, is simple to stay away from, but none-the-less a number of chopper pilots with non-rigid rotor systems are killed this way: a phenomenon known as “mast bumping”. It is caused by abrupt control movements involving significant negative G excursions.
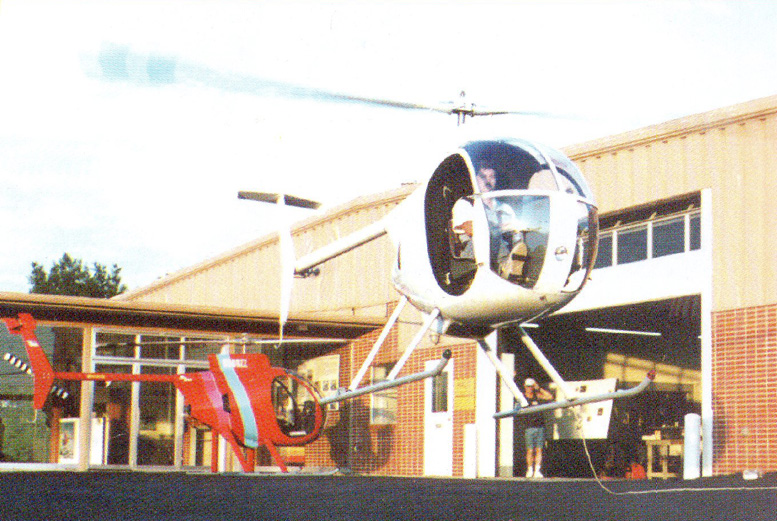
Brian Thomas, just hovering around!
The usual accident scenario involves some poor schmoe flying low until he realizes that he is about to hit something (like a power line or antenna) followed by a radical pitch up and a pitch down on the other side, thereby severely “unloading” the rotor and exerting a lot of negative G’s in the system.
Severe negative G exertions can unduly decay rotor rpm to the point where the rotor engages in a wild flapping action that can often be so violent as to allow the blades to contact the fuselage or “bump” and sever the mast.
This will ruin your whole day… and every day thereafter. It’s not at all difficult to avoid; it is just common sense, but every now and then some inattentive cowboy kills himself this way…and it doesn’t need to happen.
Now that I’ve probably scared you off from the whole helicopter idea, let me also add this: helicopter flying is exhilarating, fun, not that hard to learn (if you’re patient), and the capabilities are outstanding.
The first time you get to hover around on your own and do a near-vertical lift-off from an area that no airplane could hope to get out of, or land in a parking lot somewhere (where allowable) to make a meeting, you will understand just how versatile and powerful a tool the helicopter can be.
Believe me, some many hundreds of helicopter hours later, I’ve enjoyed this skill thoroughly, and recommend it highly.
Where Were We? Oh, Now I Remember: The Flight Report.
Before long. I was feeling my oats and having a ball.
The responsive nature of the Mini 500 helicopter rather invites a small amount of showing off. I executed a few coordination maneuvers to fine-tune my reactions and was pleased with the result-especially flying a pattern whereby I flew a 30-ft-wide circle with the nose always facing the inside of the circle.
Sideways translation revealed no undue control responses and the bird remained fairly stable in sideways translations that pushed 10 kts. Rearward flight went equally well, as long as I kept the speed low enough to keep the T-tail from fighting me. Rather than just hovering down to the end of the runway for some high speed runs.
I set up a 10-ft hover and hover-taxied down at 10-15 kts, often rotating 360 degrees while still traveling the requisite direction. Upon reaching the end of the runway, I would allow the machine to slide to the side and pivot 180 degrees in a fluid motion that felt pretty daring.
The cyclic response profile, by then, was really beginning to feel friendly and I was definitely having a good time. About this time, I was feeling like “Ace, the Chopper Jockey” and that should have warned me of what was to come.
Thud! Screw-Up ‘R Us!
I did pull a fairly good screw-up that demonstrated the more forgiving side of Revolution’s bargain mixmaster: During a slow downwind hover-taxi, I flew behind a tree-line and let the rotor rpm decay to 90% through shear stupidity.
As I finally noted the Mini 500 helicopter low rotor speed (Earth to Zoomer, Earth to Zoomer… you’re about to screw-up, you bozo!), I added collective to avoid settling while wrapping on the throttle hard… too late!
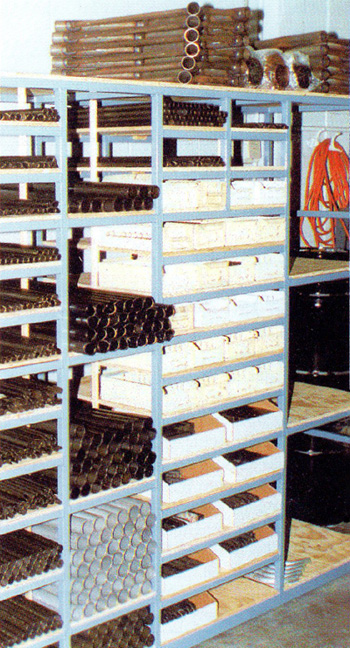
Tube be, or not tube be… (sorry, I can’t resist bad puns and they’re not yet a capital crime here in Florida).
Hovering is the most power-consumptive process in helo flying, and thinking ahead is every bit as necessary during the relative “safety” of a low-altitude hover as it is anywhere else.
Unfortunately, my brain had gone to lunch and forgotten to tell me I was on my own. The rotor rpm quickly decayed to 80% and even a quick temporary release of the collective was not enough to bring it back before a “landing” was imminent.
Just prior to touchdown, I decided to allow the bird to continue transitioning slightly forward for a “run-on” touchdown (being downwind) and yanked the collective at one foot for a fairly soft landing… though the soft and tall grass along-side the taxiway slowed me a bit faster than I expected and I rocked a fair amount forward on the skids before coming back to level position.
I might add that when caught by a significant tailwind, the T-Tail is pushed up slightly and one may have to counteract a slight pitch negative input.
There is more than sufficient cyclic control to contend with this and the problem is little more than a slight nuisance. Guess how I found that out? Anyway, it wasn’t a totally bad touchdown, but it was very sloppy and the true credit for the resultant success of this maneuver has to be the machine’s.
I had gotten way too cocky and was asleep at the switch. For low-altitude hovering, one really needs to keep the rpm up, as once the rpm hits the wrong side of 90%, you either have to lower the collective to gain a small mechanical advantage while the engine catches up… or land.
Being too low, I landed (nothing quite like running out of altitude, rotor rpm, and ideas all at the same time, eh?). Cruise flight, of course, makes this (slight low rotor rpm) only a temporary set-back, since a slight lessening of the collective or a slight aft cyclic load will bring up rpm readily.
Later, I allowed rpm to decay to 90% while booking along at 65 mph and found that getting rotor rpm back came readily with just a little aft cyclic and only minimal speed loss (less than five kts).
By the way, the Mini’s gear is very sturdy; I should have spread the skids as wide as the Grand Canyon, but they held very well (think God I did this BEFORE lunch… I shudder to think what might have happened otherwise… BOOM!).
I was also watching the rotor disk carefully, as the low rotor rpm and high descent rate is just begging for a boom strike and I was pleased to see more than adequate room exists for slight rotor disk excursions. Yup, I’m impressed.
The Revolution is a very forgiving little helicopter… which is just what it is going to need to be. The Mini 500 helicopter is no slouch in the speed department… and Revolution may even have underplayed the potential of the aircraft in this regime.
I saw Brian Thomas cruise around the pattern at Oshkosh well in excess of 100 mph on several occasions and the bird was recently clocked by a police radar gun at over 111 mph. Regardless, they’re sticking to the 95 mph cruise numbers right now and I have no doubt that those are more than reliable.
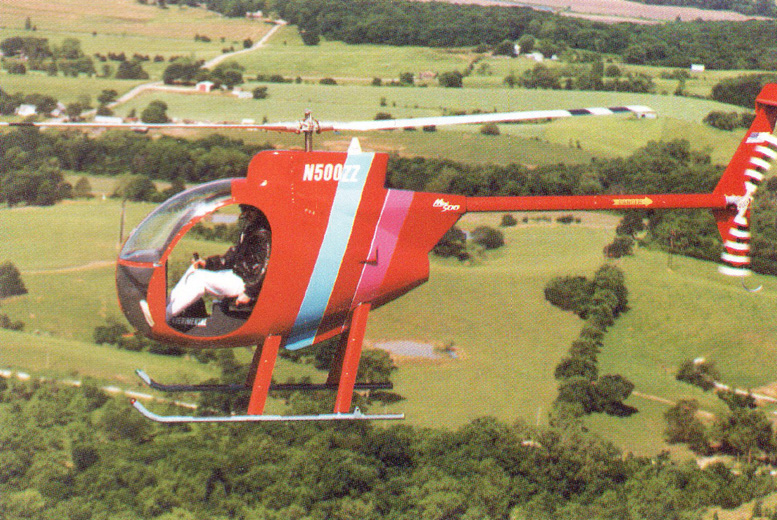
Chief Test Pilot, Brian Thomas, has already demonstrated a top speed of 111 mph!
The Mini 500 helicopter experiences translational lift effects at a pretty low speed-about 12 to 15 mph-and while there is a slight shudder as you kick on through, the aircraft’s basic trim is undisturbed (unlike a few larger piston machines that do a fair amount of wallowing/pitching in this process).
Power requirements thereafter are minimized significantly. One finds a slight need for a bit of right cyclic input to maintain straight-and-level until you hit 50-60 mph, by which time the left leaning tendency has pretty much disappeared.
Incidentally, the Mini 500 helicopter is supposed to climb at over 1000 fpm and while I did not get into any extended climbs, this is another spec you can take to the bank: even with my fat buns in this critter, we were climbing very well indeed.
At 75-80 mph, there is moderate control damping and the bird handles very well… the T-tail doing an excellent job of offering a fair amount of directional stability in the yaw axis and in pitch as well. I was particularly impressed with the lack of pitching action associated with significant power corrections.
The Sound Of Silence
Obviously, the Mini-500’s power-off characteristics were a critical concern to me. Whether or not the Rotax is up to the job is truly inconsequential; pilots will still run out of gas, oil, or sense and wind up riding the “Pinwheel Express” (ever watch a pinwheel spin to the ground? That is autorotation, of a sort) to terra-firma sooner or later.
The Mini has a fairly high mass inertia rotor system, meaning that it will give up its rotational energy reluctantly and regain it slowly. There are advantages and disadvantages to high and low mass inertia rotor systems (for instance, the R-22 has a low mass system; the Bell Jet Ranger’s is very high).
In this case, the relatively forgiving high mass inertia of the Mini seems to be the best bet… since I have a feeling that many lower-time pilots will be transitioning to the bird.
These folks may be a little slow in recognizing the need for responding to an engine failure. In that case, the Mini’s rotor rpm will decay on the slow side and give the errant chopper-jockey a chance to realize his mistake and take action.
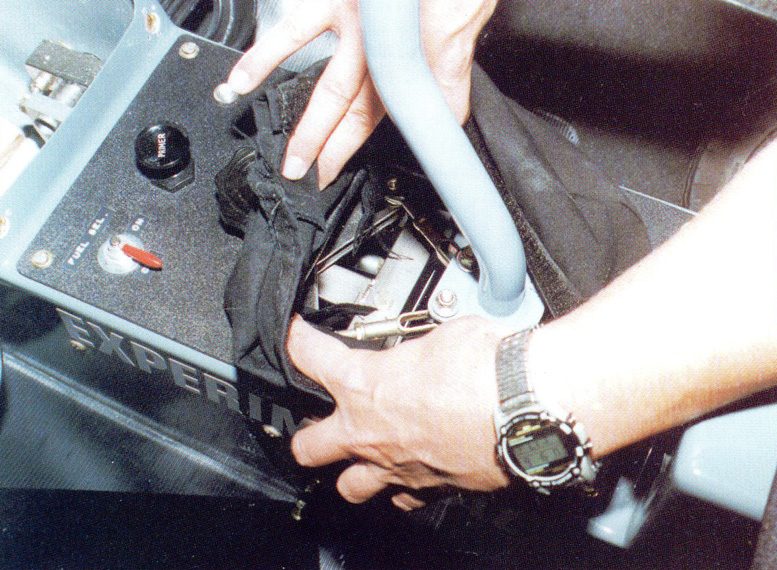
A small fabric boot at the base of the cyclic control stick offers easy access for pre-flight inspection.
Do keep in mind that once you lose that energy, it’s going to be a mite hard to get it back. I have seen hovering autorotations performed as high as 15 ft without any problem and I personally found myself quite comfortable in the 5 to 10 ft range.
There is little pitching associated with a power-cut and the Mini 500 helicopter really holds its energy well. An autorotation approach of about 55 mph will be great and you’ll probably have to bring the collective up a bit to keep the rotor rpm down to the top of the green arc. I did.
The rotor retains energy so well that most “quick-stops” virtually require you to idle the engine to keep the rpm from going to the moon, and it also helps to think ahead because the bird has enough energy to overshoot an intended point of touchdown quite readily, especially in the quick-stop.
All my autorotations were to a full hover, as no run-ons were needed because of the excess energy. I often had to pull on a fair amount of collective throughout the approach to keep the rotor from turning up too much.
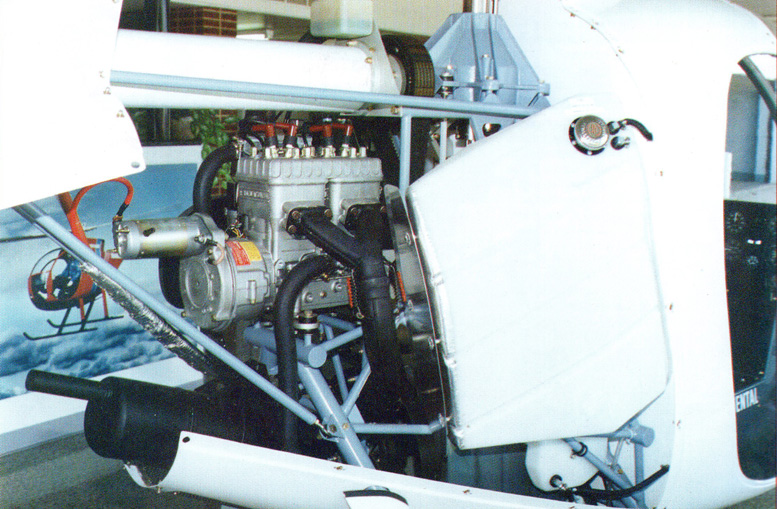
Note the 14.7-gal fuel tank on the right side of rear compartment. The Rotax, behind It, has electric start and a well-designed exhaust system.
Well, I had to cut my flying shorter than I wanted to because of a slight bit of necessary preventive maintenance (some harmless fuzz in the tail-rotor gearbox, as it turns out, but it didn’t hurt to check… those chip lights work well). I intend to go back and beat this machine up a fair amount more.
All in all, the Mini’s a pretty good effort in anyone’s book; it seems well-suited to the fact that sooner or later, a few novice boneheads (like a certain Aero-Editor who shall remain nameless) will get a hold of one of these. This bird will definitely do its best to cover your butt if you get somewhat stupid. The Mini-500 was worth waiting for.
Test Pilot’s Summary
On the distaff side, there is little to say about the Mini-500… but time will tell. Until a few dozen machines get into the field, get flying, and build up a fair amount of flight time, there is no telling whether Fetter’s laudable effort to “bullet-proof” his helicopter has paid off.
The high-time machine has over 160 hrs, has needed very little maintenance. is flying very well, and outside of some harmless “gear fuzz” in the tailrotor gearbox (normal and easily flushed out with a replacement of the lubricant), has offered few unforeseen “FUBAR’s”.
I have good vibes about what they’ve done with this design, and can verify that there has indeed been a significant effort to guard against airframe failures and component difficulties one can plainly see that Revolution is doing everything they reasonably can to safeguard their bird, and their customers, from potential harm.
Mind you, the unforeseen can still happen (just ask the incomparable Frank Robinson, who, despite being one of the world’s finest helicopter designers and engineers, still had some pretty heartbreaking teething problems with some of his early R-22’s and even the amazing R-44).
The machine flies very well, especially in a number of critical flight regimes. The power-off characteristics seem quite good and the mass inertia of this rotor system gives a sloppy pilot a few seconds to get his act together before his or her rotor rpm heads for hell.
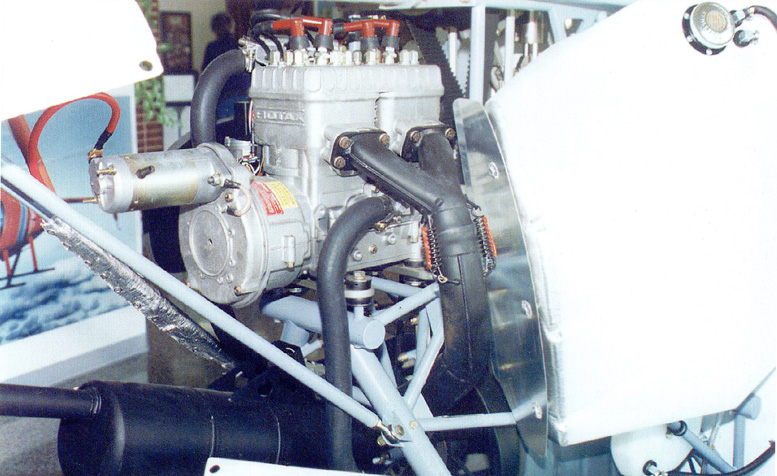
Power comes courtesy of a single two-stroke Rotax 582 with dual CDI ignition.
Inflight handling is docile and outside of some light sensitivity in the hover and a significant tendency to weather-vane in windy conditions, the bird really does very well… and I’d feel reasonably comfortable with any certified helicopter pilot getting in one as long as they are willing to spend an hour or two learning the ropes in a careful, methodical manner.
The quality of workmanship seems high; the engineering seems more than up to snuff; the early look I’ve had at the company’s documentation package appears quit e promising (probably because of the aforementioned Brian Thomas, a very experienced helicopter instructor, is responsible for that part of the Mini-500 program).
The real potential problem I see for the Mini-500 has more to do with its pilots than with the machine. Helicopters can be horribly unforgiving of carelessness and outright deadly if you take them with anything less than professional seriousness.
If all of Dennis’ customers behave like professional helicopter pilots, he’s gonna do fine (and mind you, he just won’t sell the bird to inexperienced helicopter pilots until they prove themselves).
However, if the sport plane game has taught us anything, it’s the fact that a fair percentage of our brethren still insist upon not listening to reason and doing their own thing, no matter how fool-hardy that might be.
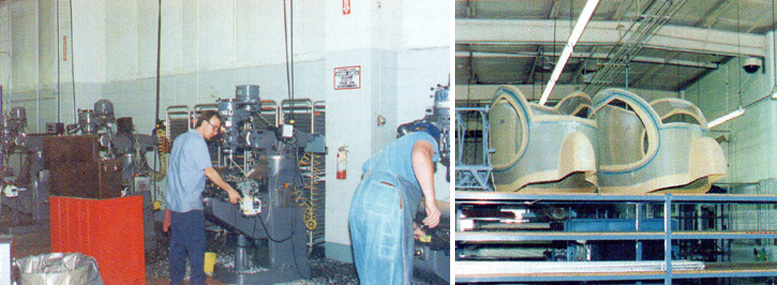
LEFT: Busy, busy, busy: Revolution is now tooling up for full production and hopes to have most, if not all, of the first 25 ships out the door by New Year’s Day.
RIGHT: Lots of parts are being built and readied for shipment… Mini-500 orders now stand at nearly 300 birds!
A few of them might get themselves killed in the Mini through no fault of the machine (these same guys could also kill themselves in R-22’s, Hughes 300’s, ultralights, Cessnas, you name it). – EDITOR: The irony here is this article was written in 1994, we were later to learn that there were a number of issues yet to be sorted out with the earlier Mini 500 helicopters, resulting in more than 10 deaths as a direct result of the machine, not the pilots…! A number of upgrades were to follow.
I hope that Dennis’ efforts to screen and warn these people is taken seriously by his clientele, as the pay-off is incredible: a lot of fun flying in an insanely affordable machine (as far as helicopters go).
To be truthful, until I saw this thing fly so aggressively at Oshkosh and then flew it myself, I was fully expecting, somewhere down the road, to be writing less-than-flattering things about Fetters Mini 500 helicopter and company.
I blew it, Dennis-you did what you had to do and my hat’s off to you. The Mini 500 helicopter is the most fun, I’ve had so far in a sport plane in 1994, bar none (and mind you, 1993’s winner was the BD-10!). Don’t be surprised if you hear I bought one.. I liked it that much.
Mini 500 Helicopter Specifications | |
---|---|
Height | 8′ 1"h |
Length | 22′ 6" |
Width | 5′ 3" |
Cabin Height | 52.75" |
Cabin Width | 34.5" |
Cross Weight | 840 lbs |
Empty Weight | 485 lbs |
Useful Load | 355 lbs |
Mini 500 Helicopter Main Rotors: Two composite with aluminum leading edge, semi-rigid rotor system |
|
Normal Operating Range | 550 rpm |
Diameter | 19 ft |
Blade Chord | 8 inches |
Tip Speed @ 100% rpm | 547 fps or 373 mph |
Mini 500 Helicopter Tail Rotor: Two metal blades |
|
Normal Operating Range | 2671 rpm |
Diameter | 3 ft 10 inches |
Blade Chord | 4 inches |
Tip Speed @ 100% rpm | 536 fps or 365 mph |
Mini 500 Helicopter Engine: No Options |
|
Rotax 582 | (liquid-cooled, dual-ignition) |
Horsepower | 67/6500 rpm |
TBO | 500 hrs |
Fuel Capacity | 14.7 gal. |
Mini 500 Helicopter Performance: Verified |
|
Max cruise Speed | 95 mph |
Cruise Speed | 75 mph |
VNE | 150 mph |
Rate Of Climb | 1100 fpm |
Max Range @ Cruise | 225 stm |
Endurance | 3 hrs |
Service Ceiling | 10,000′ |
Hover in Ground Effect | 7000′ |
Hover Out Of Ground Effec | 7000′ |
Build Time | 40 to 60 hrs |
Original Cost | $24,500 (As of initial release time; subject to change without notice) |
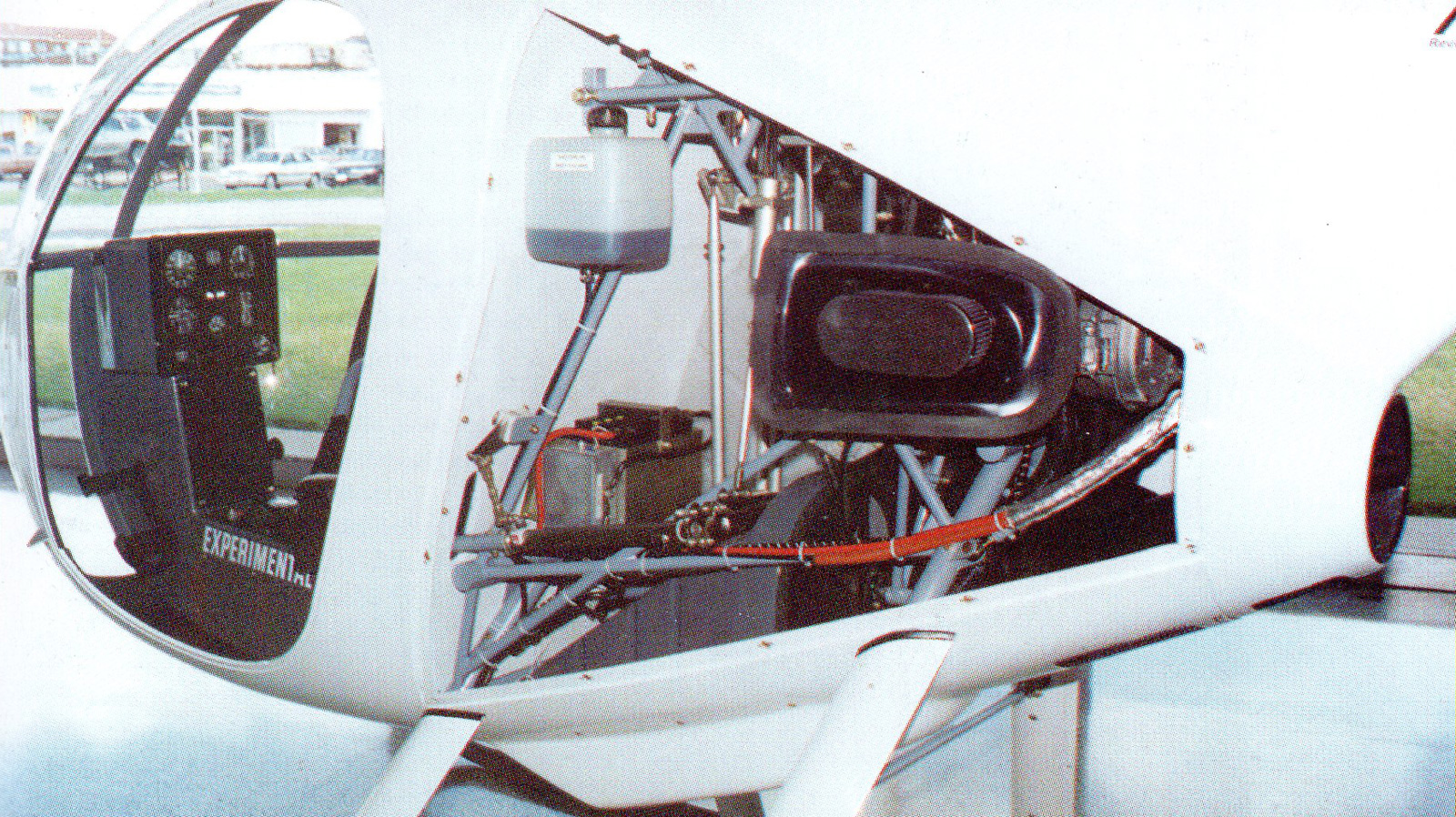
Be the first to comment on "Mini 500 Helicopter Flight Test"